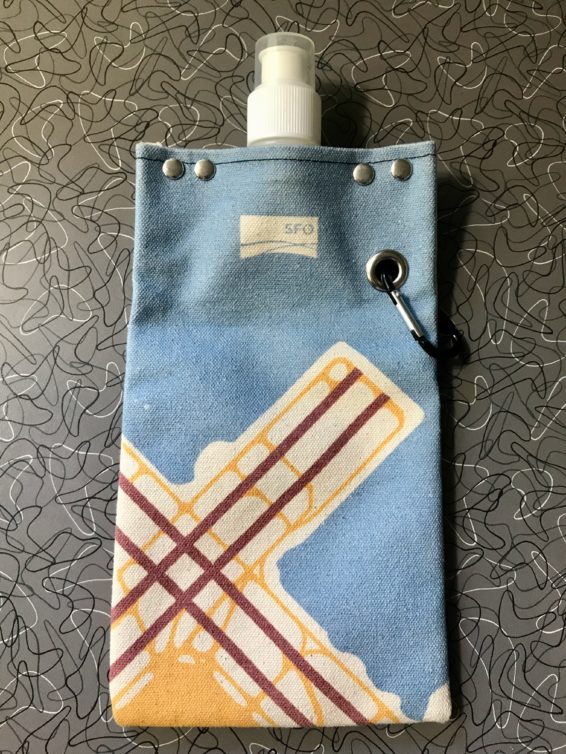
A SFO-branded reusable water bottle. This is probably a good enough reason to never use a plastic water bottle again. – Photo: AirlineReporter
First off, let’s be clear, I like the environment and want to not only do my part to make sure we have a nice little planet to live on, but also to motivate others. However, the plastic water bottle sales ban at the San Francisco International Airport (SFO), taking effect on August 20th, got me thinking. Do these sorts of changes work as well in a ’œtrapped’ world, like an airport? I say that since people in an airport do not have as much choice’¦ they mostly can only pick among the options given to them on the airside (after security).
Over the years, airports have grown the choices airside by leaps and bounds. Heck, many airports are more like shopping malls than an airports. But in the end, you are limited. If your local grocery store decides to no longer sell a product and it is super important to you… cool, just go down the street to the next one. At the airport, that is going to be a bit more of an ordeal.
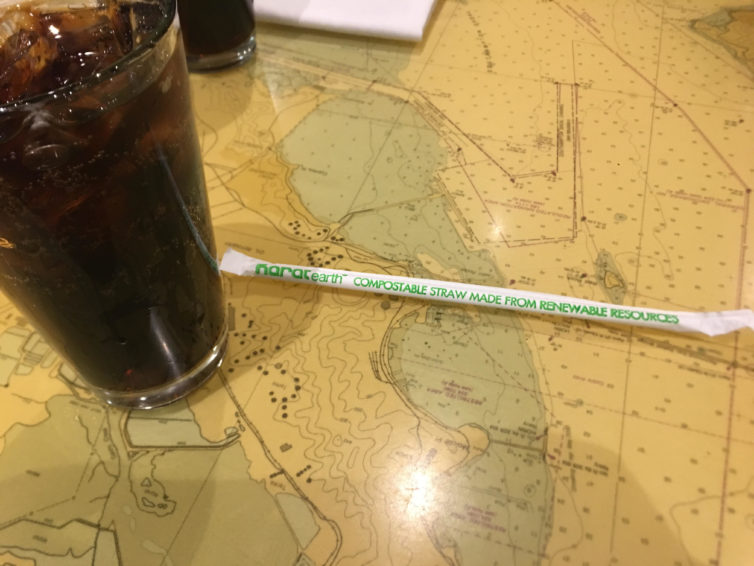
My paper straw that I got to try while flying through SFO last time – Photo: David Parker Brown
I will say that I was shocked by some of the numbers. On average, SFO sells about 10,000 plastic water bottles per day, and that equals 3,650,000 per year. No question that is A LOT of plastic and even if they are all recycled (saying they are being recycled), it is not a good thing for the environment. It actually makes me pretty sad so many people do not bring their own reusable bottles (my fianc brings one for both of us and is always reminding me to hydrate). Conversely, that high number of bottles also shows there is A LOT of demand from people to drink water in plastic bottles. Is it fair to require passengers to use other options?
Sure, sure, getting a reusable plastic bottle is not that much to ask, and the airport is providing some other good options, including water in other packaging (like aluminum and glass). But how expensive will those be and how will that impact a family of four on a fixed budget? Will passengers accept the change? Should there be some line of convenience vs doing what’s right, and is this new policy crossing it? Honestly, I don’t know the answers. But let me share with you some of my thoughts and I hope that we have a good conversation in the comments…
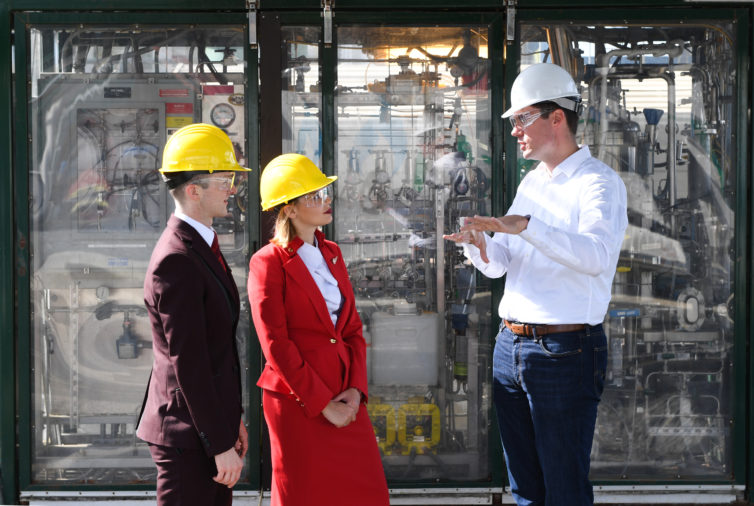
Photo: Doug Peters/PA Wire
It can be hard for the environmentally minded AvGeek to get on a flight without a twinge of guilt, since planes spew tons of carbon dioxide into the atmosphere every minute of every day. Over recent years, the industry has slowly started wising up to the importance of sustainability. We’ve seen some airlines introduce biofuels derived from plant products. But today, the field takes a new leap forward.
The Boeing 747 flying Virgin Atlantic’s flight #16 today from Orlando to London Gatwick will be powered by a unique sustainable jet fuel that’s recycled from carbon-containing waste gases from industries like steel mills. The result is a product that has proven at least as powerful as regular jet fuel but with a significantly lower carbon footprint. The flight is the outcome of a partnership between Virgin Atlantic and LanzaTech, which developed the fuel. Partners like Boeing, Honeywell, GE, fuel suppliers, and the DOE played a significant role as well.
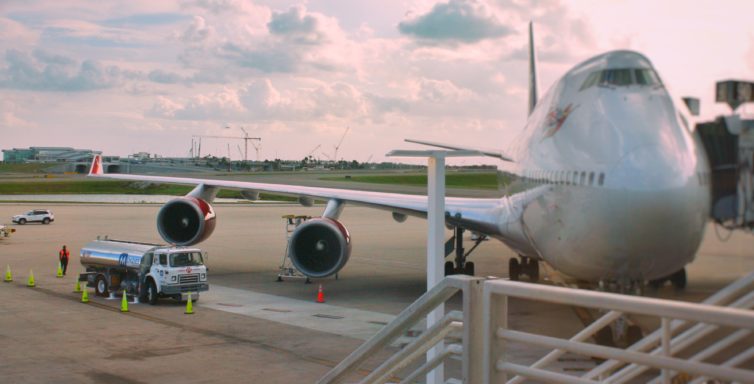
The star of the show. Or stars, if you include the fuel tanker. – Photo: Manu Venkat | AirlineReporter
We’ll be on the inaugural flight and will be back later with a full report. For the time being, check out our Twitter feed for live updates. Here’s to a greener future for aviation!
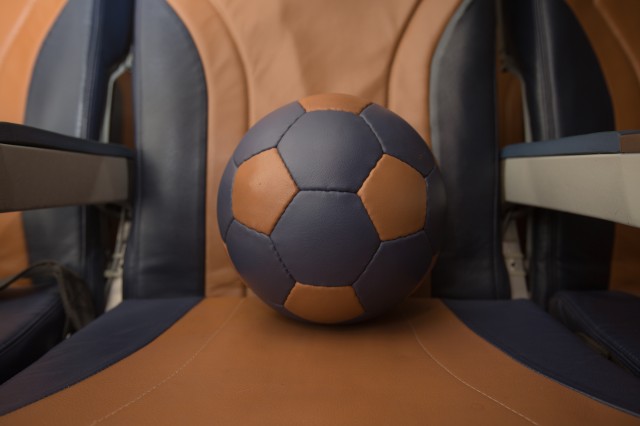
Turning leather seat covers into soccer balls; part of Southwest’s new LUV Seat program – Photo: Southwest Airlines
When you think about recycling in the aviation industry, most folks think of the aircraft that are scrapped and recycled. Some airlines will recycle the cans and cups onboard that get used, but that seems to be the exception rather than the rule. However, what about something on a different scale? Two programs have been launched this year that take different approaches to using up leftover materials and recycling them into something useful – something that will help people, not just the company’s bottom line.
In July of this year, Southwest Airlines launched their ’œLUV Seat’ program, or as the motto puts it ’œRepurpose with a Purpose’. Labeled more as “re-purposing” than “recycling”, the program is designed to take the leftover leather from Southwest seat refurbishments and turn them into usable goods.
The first of those materials is heading to Africa, where seat leather will be turned into soccer balls, shoes, and other items. They don’t call it “recycling” – they call it “up-cycling”. Turning unwanted items into higher value products.
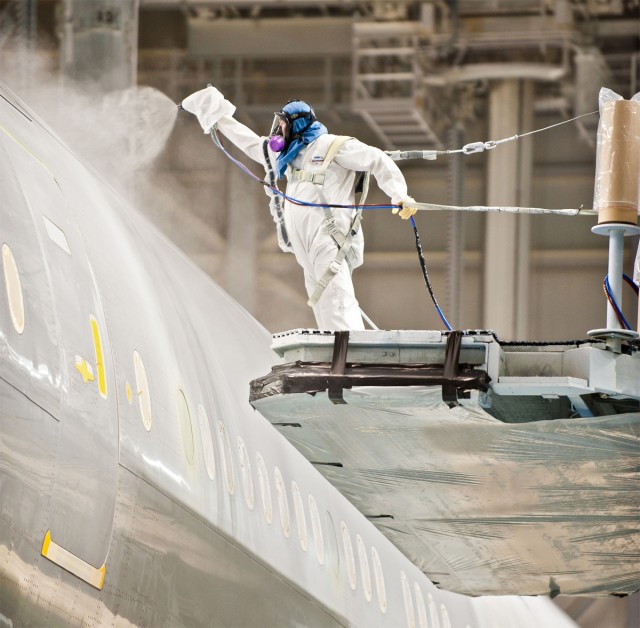
Boeing painter Bill Pearson applies chrome-free primer to the 777-300ER that was delivered to Air New Zealand in November 2011. Photo from Boeing.
Boeing has announced 10 initiatives on the 777 program that will help to eliminate 5.5 million pounds of CO2 and 300,000 gallons of jet fuel per year just in the 777 delivery process.
A lot of attention is given to how airlines can save money and the environment when flying them, but how about aircraft manufactures saving a little green (money and environment) before an aircraft is even delivered?
Before each 777 is delivered, there is a 20-day process of paint, tests and flights before Boeing hands over a brand plane to a customer. Boeing has been working on creating a more efficient process with Air New Zealand, which took delivery of a 777 using all ten initiatives.
“A team of employees identified redundancies in testing,” said Jeff Klemann, vice president Everett Delivery Center stated in a press release. “One idea was to eliminate engine-run tests already performed by GE, the 777’s engine manufacturer. This will result in a reduction of 1.4 million pounds of CO2 in 2012 as well as less community noise and emissions.”
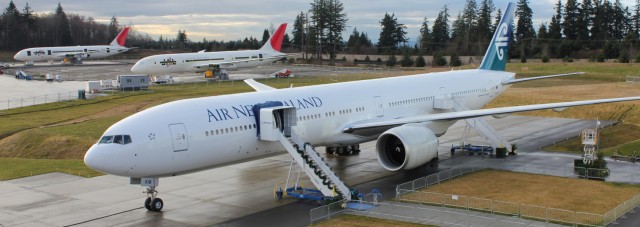
In December 2010, Air New Zealand took delivery of their first Boeing 777-300ER. Photo by AirlineReporter.com.
A team of employees identified redundancies in testing and new more sustainable processes.Through out the 777 delivery process the team implemented the following 10 initiatives:
* Eliminated redundant fuel test in pre-delivery flight test
* Reduced the amount of times hydraulic filters are changed
* Eliminated engine-run tests already performed by GE
* Used waste fuel carts
* Reduced the number of times potable water is changed
* Reduced the amount of times engine fuel filters are changed
* Enhanced recycling throughout the delivery process
* Used electric carts instead of gas-powered vehicles
* Improved flight planning efficiency for pre-delivery flights to reduce fuel loads and flight times
* Used chrome-free primer
Nine of the initiatives will come standard with all future 777 deliveries. Usage of the special chrome-free paint will be an airline option.
MORE AIR NEW ZEALAND 777 STUFF:
* Behind the scenes of an ANZ 777-300ER delivery
* Checking out the interior of ANZ’s 777-300ER
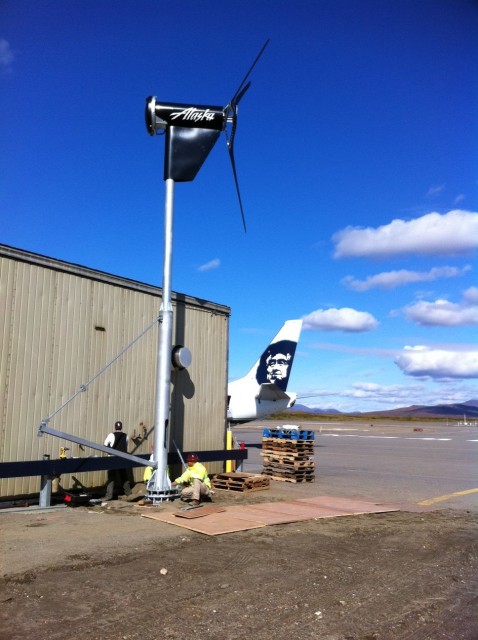
Wind power for Alaska Airlines up in Nome, Alaska. Photo from Alaska Airlines.
So where the heck is Nome, Alaska? It is pretty darn as close to the middle of no where as you can get, although it is on the western edge of Alaska. It is a small town of less than 4,000 people and transportation to destinations outside the city is difficult to come by. Roads connect Nome to smaller cities up to 54 miles away, but there are no roads connecting the city to the rest of the world. For the town to operate, it requires transportation via water and air.
Air travel becomes a necessity to get goods and people to and from remote areas in Alaska and Alaska Airlines is one of a few airlines operating out of Nome ’“ it is also the largest.
Nome has long days in the summer, short in the winter and is the end destination of the Iditarod dog sled race. The remote city is also known for its fierce winds of 80 to 90mph. With being so remote, having strong winds and long days of light in the summer, it makes sense for locals to look at alternative sources of energy and that is just what Alaska Airlines has done.
Recently the airline built a 30-foot wind turbine next to the Nome Terminal and installed solar panel array on the roof. According to Alaska, ’œthe project is the first foray for Alaska Airlines into using wind and solar power to produce a significant amount of an airport’s electricity ’“ and it appears to be the first time a domestic carrier has pursued alternative energy for an airport operation.’
Alaska is hoping that the turbine and solar panels will produce around 15,000 kilowatt hours of power per year, which is about 6 percent of the terminal’s load. If successful, the concept may be expanded to other rural airports in Alaska, said Ron Suttell, Alaska’s director of facilities planning and administration.
“The turbine was selected because it performs well in turbulent air, it is engineered to continue producing electricity in harsh climates and high winds, and the design eliminates icing issues on the blades,” Chris Andree, Alaska Airlines’ regional manager of properties and facilities, who oversaw the project for the airline.